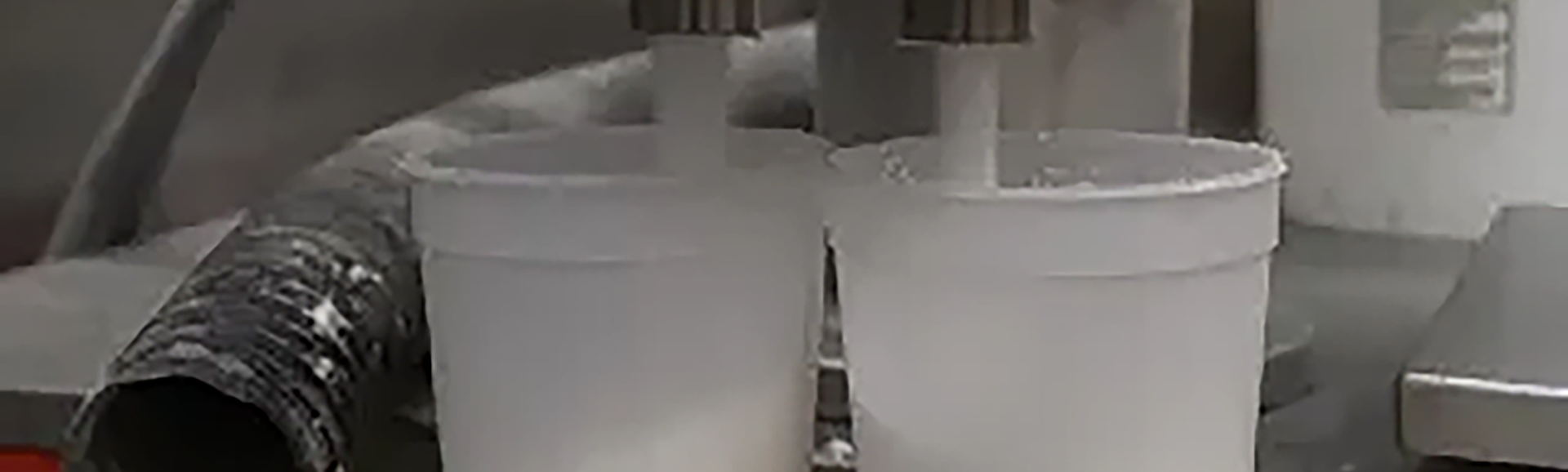
Packaging Rates and Container Sizes: A Crucial Correlation
Often the size of the container opening is overlooked, yet it plays a critical role in determining the achievable rate per minute
In the packaging and filling machinery industry, many factors influence the efficiency and productivity of filling processes. Often the size of the container opening is overlooked, yet it plays a critical role in determining the achievable rate per minute, directly impacting overall throughput and efficiency.
Physical Limitations on Auger Tooling
One of the primary reasons the container opening size can make or break the achievable rate per minute is due to its physical limitation on the size of auger tooling that can be used. When the container opening is smaller, the auger tooling must be reduced in size to fit through the opening and prevent spillage. In contrast, larger openings can accommodate bigger augers, allowing for more product to be delivered per rotation and enabling higher operating speeds, which ultimately boosts the filling rate per minute.
Consider a typical scenario in the powder filling industry. When filling containers with a standard opening size of 50mm, the filling machinery can achieve a base rate per minute. However, if the opening size is reduced to 30mm, the auger tooling must be reduced in size to fit through the opening. This smaller auger delivers less product per rotation, creating a slower filling process and resulting in a lower rate per minute. Conversely, increasing the opening size to 70mm allows for the use of larger augers, which can deliver more product per rotation and operate at higher speeds, thereby significantly increasing the filling rate per minute.
STRATEGIES FOR OPTIMIZATION
To optimize filling rates, a few strategies can be employed.
1. Standardizing Container Designs
Where possible, standardizing container designs with optimal opening sizes for packaging (where possible) can streamline the filling process and maximize efficiency.
2. Tooling Selection
Properly sized tooling is essential to ensure the material is dosed at a rate that allows it to drain freely from the collector funnel without clogging. Free-flow products being filled into containers with small openings can achieve slightly improved rates by increasing the size of the free-flow tooling to reduce cycle time. This method permits the use of tooling larger than the container opening, which enhances fill speed since the material flows freely. Tapered tooling can be utilized under specific circumstances to increase the rate in non-free flowing materials but can cause heat generation and jamming of the tooling. To learn more about free-flow and non-free-flow materials, see our video here.
Conclusion
The size of the container opening is a critical factor that significantly influences the achievable rate per minute in filling operations. By understanding and optimizing this variable, manufacturers can enhance their filling efficiency, reduce production time, and increase overall throughput. As the packaging and filling machinery industry continues to evolve, staying attuned to these details will be key to maintaining competitive advantage and operational excellence.