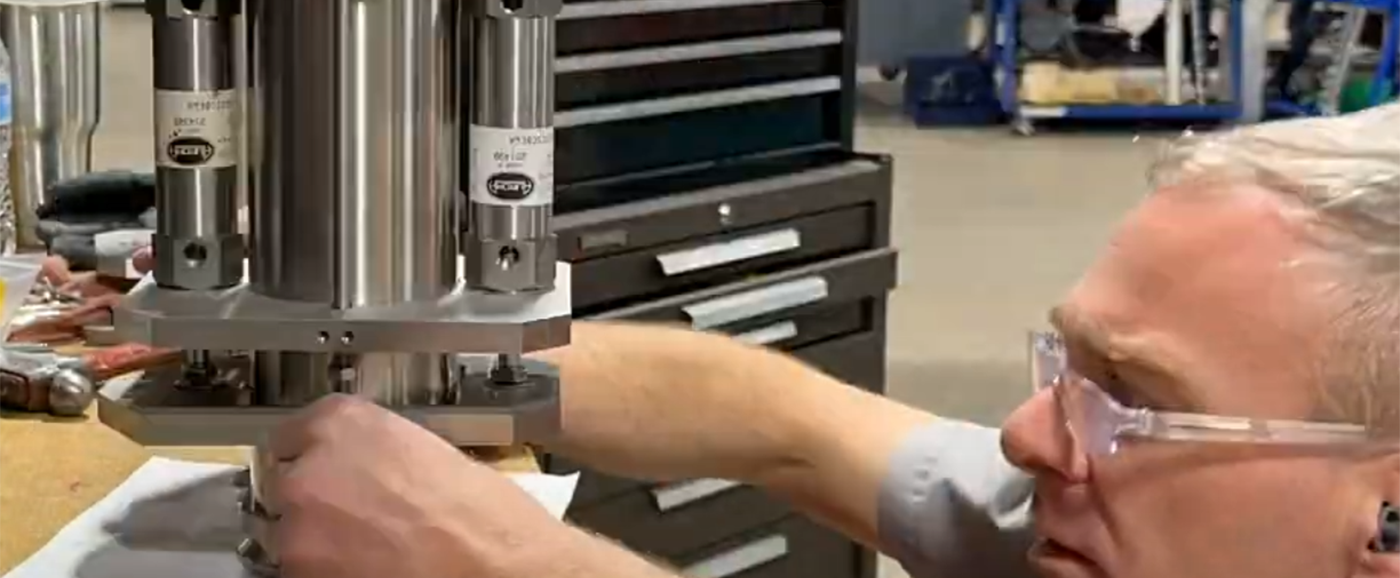
STOP THE DRIP: TOOLING ADDITIONS FOR ADDED EFFICIENCY
Decrease waste in your non-free flow product line with these tooling suggestions.
Greater efficiency, less waste, and cleaner filling environments are important benchmarks with which to evaluate your packaging process. With non-free flow powders, however, the product characteristics could be susceptible to drip: when product falls from open-bottom tooling even after the filling cycle. This could cause multiple problems in your packaging, but our Lab Technician, Chris, has solutions.
View our selection of cutoff devices here>>>
Drip Mitigation Methods
When working with non-free flow powders, preventing drips from the open bottom of standard tooling is essential for maintaining accuracy and a clean filling environment. Because these powders don't flow freely but can fluidize after dosing, they may continue to fall after the cycle completes. Fortunately, several solutions exist to control and minimize the issue.
-
DRIP WASHERS: Controlling Flow with Restriction
Drip washers are flat washers featuring a chamfered relief on the upper side, forcing product to navigate around them before exiting. Their diameter is tailored to the tooling size, with larger washers providing stronger drip mitigation. However, excessive restriction can create backpressure, potentially generating heat or, in extreme cases, causing auger jams.
-
GRID RESTRICTORS: Disrupting Product Flow
Grid restrictors use metal wire arrays arranged in different patterns - grids, circular designs, or pie-shaped sections - to help restrict flow. Grid restrictors help slow material movement reducing the likelihood of drips. However, if too restrictive, they can create backpressure on the auger tooling , leading to heat buildup or potential jams, just like drip washers.
-
POSITIVE CUTOFF DEVICES: The Most Effective but Costly Solution
A positive cutoff device physically blocks product flow after the desired dose has been dispensed, making it the most reliable solution for drip prevention. This approach is especially useful for powders prone to fluidization, as it completely stops excess material from escaping. These devices typically use a blade, valve, or flapper mechanism to achieve a clean cutoff. However, while highly effective, positive cutoff devices are also the most expensive option.
-
REDUCING TOOLING SIZE: The Simplest Fix with a Tradeoff
In some cases, using a smaller tooling opening is enough to reduce or eliminate drips. By decreasing the available space for product to flow through, the natural tendency of material to continue falling is minimized, offering the most cost-effective solution. However, the tradeoff is a reduced rate per minute, as smaller tooling slows the delivery of product into the container.
CHOOSING THE BEST METHOD
Each of these methods provides a unique approach to drip mitigation. Drip washers and grid restrictors offer passive control but must be chosen carefully to avoid over-restricting flow. Positive cutoff devices are the most effective but come at a higher cost and added complexity. Reducing tooling size is the simplest and least expensive option, but can impact production speed.
By understanding how each of these solutions functions, operators can ensure more precise, cleaner, and more efficient powder filling while balancing cost, speed, and effectiveness.