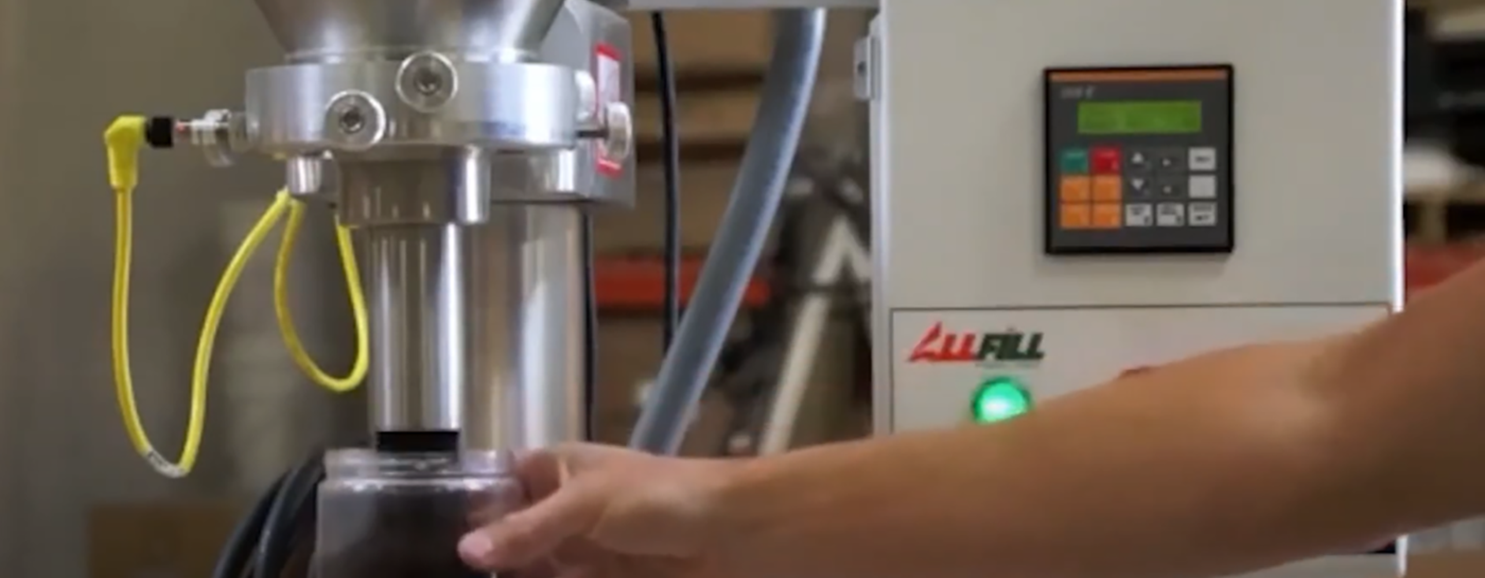
'TWEENER' PRODUCTS: A UNIQUE TOOLING CHALLENGE
A tweener possesses both free-flowing and non-free-flowing characteristics, depending on its state of agitation or aeration.
Imagine a powder or granular substance that seems to have a mind of its own. Picture a jar of baby powder or foot powder. When untouched, it maintains a compact, non-free-flowing state. However, give it a shake or puff the container, and suddenly, it flows like a waterfall, becoming fluid and free-flowing. This tricky product characteristic is what we call a "tweener". A tweener possesses both free-flowing and non-free-flowing characteristics, depending on its state of agitation or aeration.
When faced with a tweener, determining the appropriate tooling becomes a conundrum. Consider the machinery used in powder packaging, particularly auger fillers. The challenge with tweeners is that auger tooling typically only comes in two configurations — non-free-flow or free-flow (to learn more about auger tooling types, view our videos here.) The material, however, continuously oscillates between states during packaging, making it difficult to choose the right tooling. The wrong tooling causes significant consequences: inaccurate dosing, inconsistent product quality, spillage during packaging, and potential downtime due to machinery adjustments.
How do we tackle this challenge?
Understanding Material Behavior: The first step is to thoroughly comprehend the characteristics of the material in question. Conducting comprehensive testing and analysis can provide valuable insights into its behavior under various conditions. Our complimentary Test Lab will shed light on the specific characteristics of your unique product.
Utilizing Specialized Techniques: In some cases, application specifications and characteristics allow us to employ specialized techniques to combat tweener challenges. For instance, utilizing small diameter non-free-flow auger tooling can create enough compression and backpressure to keep the material in a non-free-flowing state with a manageable drip. The tradeoff with this technique is that as tooling size decreases, so does rate per minute. While it may be a better method in terms of control and accuracy, the machine is slower, increasing production run times. Additionally, controlling the amount of agitation used during packaging can influence the material's flow state, favoring either non-free-flow or free-flow as required. Running continuous agitation can sometimes keep a tweener in a free-flowing state, allowing traditional free-flow tooling to be utilized.
Experimenting with Cutoffs and Auger Combinations: Various cutoffs and auger combinations can also be attempted to control the material and accurately dispense it. By experimenting with different configurations, we can identify the most effective approach for each specific tweener product. While materials with tweener characteristics present unique challenges in powder packaging, they also offer opportunities for innovation and optimization. By understanding their behavior and employing adaptive solutions, we can navigate the complexities of tweener products with confidence and efficiency.