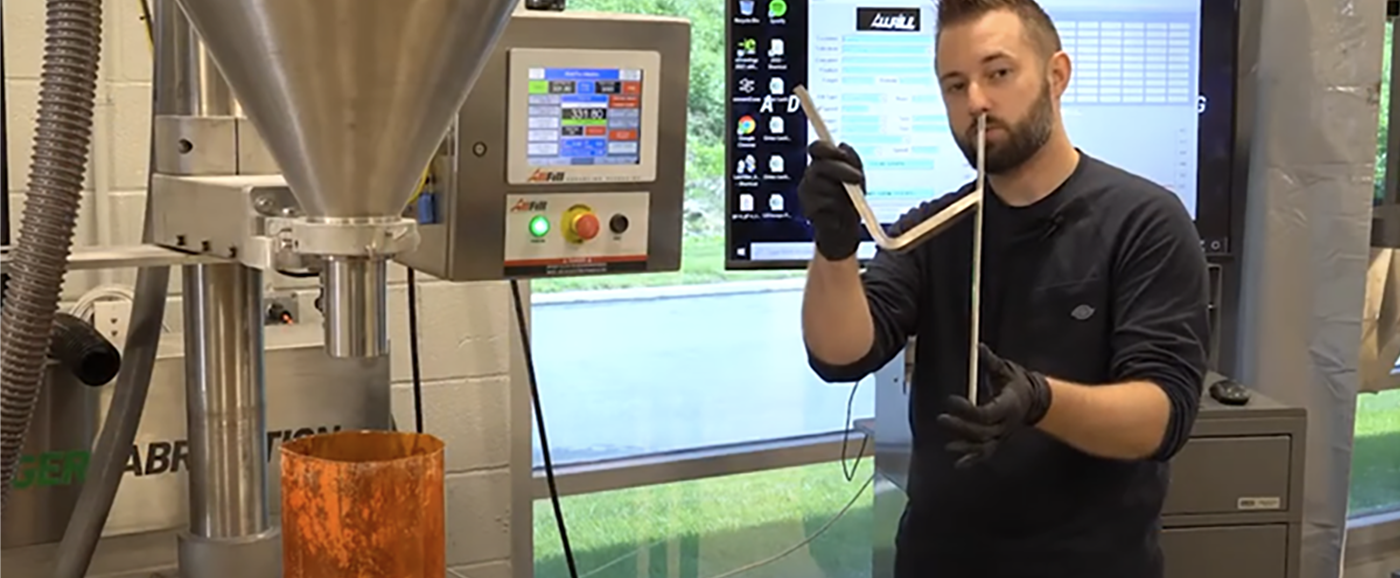
Understanding Aeration and Degradation in Auger Fillers
The key to preventing aeration and degradation.
In powder and granule filling, achieving consistent and accurate fills can be challenging, especially when the material's physical properties are altered during the process. Two significant issues that can arise are aeration and degradation, both of which directly impact production rates, product quality, and equipment performance.
Aeration: The introduction of excess air into the product, altering the density of the material before it even reaches the auger filler and leading to fluidization and unstable filling.
Degradation: The breaking down of granules through the rough handling of the product, creating finer particles that lead to material density changes and filling inconsistencies.
What causes Aeration and Degradation?
There could be many factors affecting a product during the filling process. In general, the first two aspects to check are product agitation and infeed systems.
Continuous Agitation: Many auger fillers rely on continuous agitation to keep powders and granules flowing freely. However, constant mechanical action can degrade the material over time. The resulting degradation may densify the material, causing overfilled containers or product settling, especially in fragile materials. |
The Role of Infeed Systems: Infeed systems, such as conveyors or vibratory feeders, play a crucial role in delivering material to the auger filler. Although, by moving product, they add another layer of agitation to the system which exacerbates degradation and aeration. |
|
Production and End Product Impacts
There could be many factors affecting a product during the filling process. In general, the first two aspects to check are product agitation and infeed systems.
Taste and Texture Changes:
For beverage and food products, degradation can affect how the product tastes or feels when consumed.
Baking Performance:
In the case of baking ingredients, degradation can alter how well a product bakes, potentially ruining the final product's structure or flavor.
Chemical Functionality:
Degraded chemical products may not dissolve or react as expected, which can have serious consequences in various applications.
Mitigation Strategies
There could be many factors affecting a product during the filling process. In general, the first two aspects to check are product agitation and infeed systems.
Reduce Continuous Agitation:
Use intermittent agitation rather than continuous to reduce product degradation.
Optimize Infeed Systems:
Adjust the speed and handling characteristics of infeed systems to minimize extra agitation.
Positive Cutoff Device:
A positive cutoff device seals off the auger between fills, preventing aerated product from leaking and providing better fill accuracy.
Densification:
Sometimes a material can be densified by closing off the auger tooling, loading the hopper to full head pressure, and allowing the product to sit for up to 30 minutes before production. Air will then settle out of the product and create a stable base of material in the hopper. Maintaining a consistent level of material in the hopper and keeping a “low level” higher in the hopper will also help minimize aeration.
Built-in Feedback for Micro Adjustments:
An integrated checkweigher can automatically make micro adjustments to filler settings to maintain optimal accuracy as it detects changes in the fill weights, helping ensure consistency without requiring constant manual intervention. View our checkweigher machines here.
Tooling Selection to Minimize Degradation:
Correct tooling selection can be an immense help to fight degradation. Tooling with clearance, reduced overflight, or serrated lip funnels can also help minimize degradation by reducing the forces exerted on the product.
If you are having issues with aeration and degradation, or have questions about the obstacles your product may face during the filling process, reach out to our experts! Give us a call at 610-524-7350 to schedule a product test in our Test Lab to learn more.